Kōʻula, the sixth residential tower built as part of Ward Village’s master plan for Kakaʻako, is a 41-story project featuring a column design that’s the first of its kind in Hawaiʻi, boasting distinctive undulating curves that make it stand out among neighboring buildings.
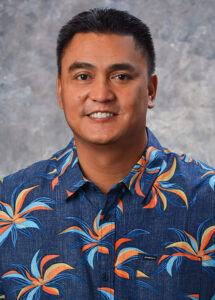
Merrill Naira
“Kōʻula has offered significant firsts for Hawai‘i construction,” says Merrill Naira, Hawaiian Dredging Construction Co. Inc. project director. “Kōʻula was the first architectural project in Hawai‘i for Jeanne Gang of Studio Gang and a first-time Ward Village project for Hawaiian Dredging.”
The mixed-use podium tower development features 942,000 square feet of built area that includes residential and guest units, common areas, amenity spaces, retail storefronts, mechanical and support space and six stories of above-grade parking.
Most of the 566 residential units are on floors nine and above, with a mechanical area on the tower’s roof.
The first seven floors of Kōula comprise parking, residential and retail spaces. An eighth-level amenity deck includes lap and family pools, recreation and entertainment areas, and dining and lounge areas. Kō‘ula’s ground level welcomes the broader community with 23,000 square feet of restaurant and retail space.
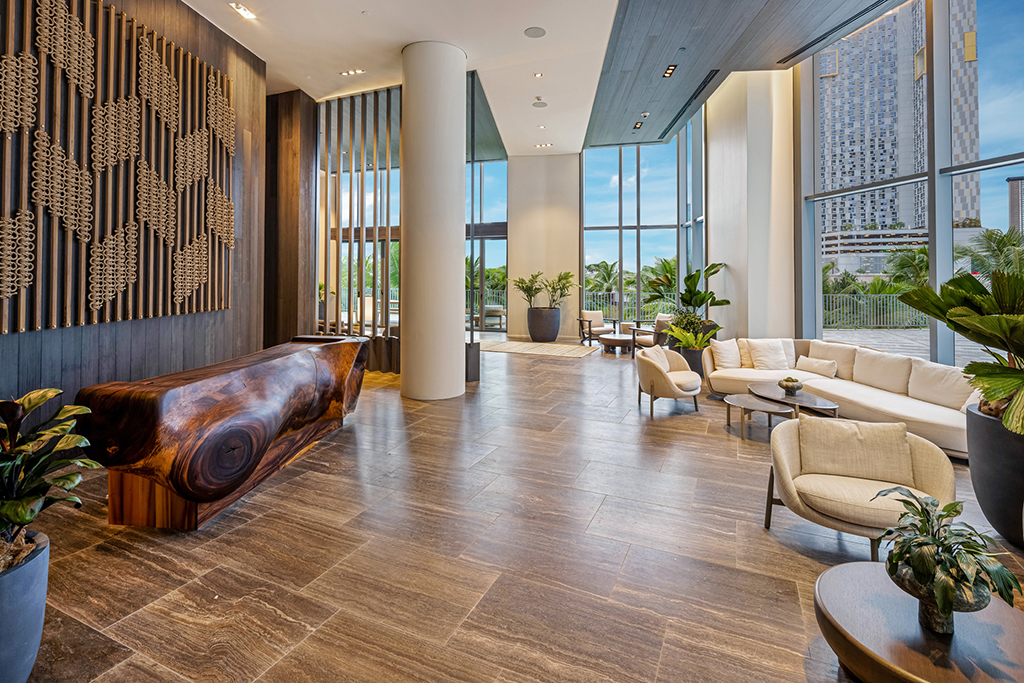
Above and below: Kō‘ula’s 942,000 square feet of built area includes lavish common areas.
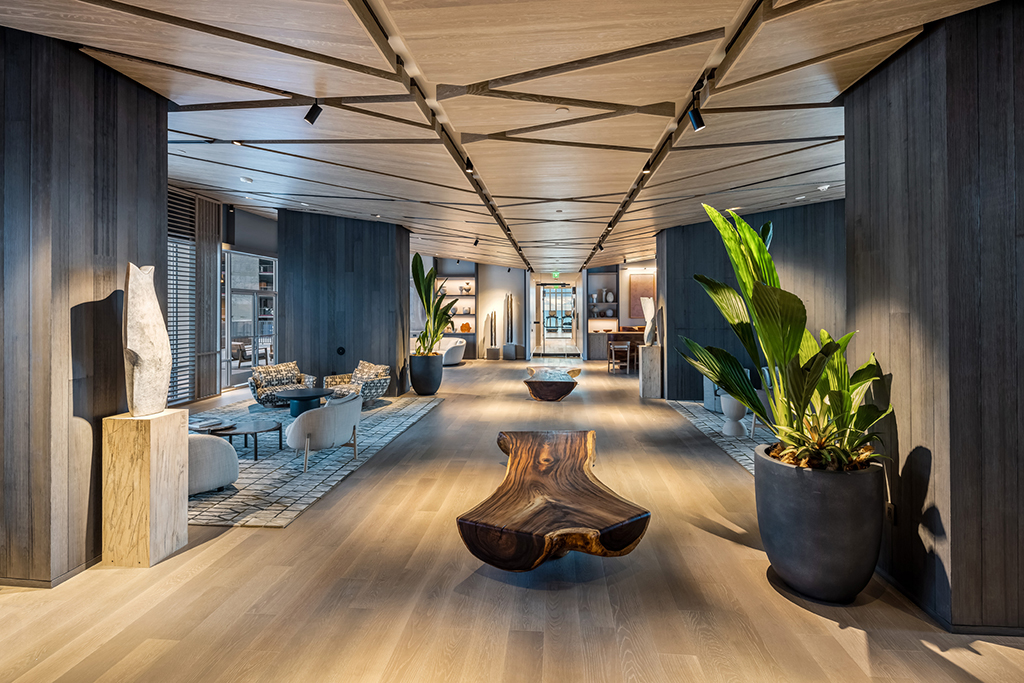
INCORPORATING SUGAR CANE INTO DESIGN
Planning, consistent communication and collaboration were crucial to completing Kōʻula’s undulating concrete facade, which pays tribute to the native grass and red sugar cane that once thrived in the area. Constructing its 400-foot columns required a strategy to integrate them within design plans for exterior window walls, balcony slab edges, balcony glass railings and unit interiors.
As flawless as the finished building looks now, the facade required an innovative approach when it came to forming the columns, Naira says. Advance testing of construction materials was crucial to the project’s success.
Studio Gang and Hawaiian Dredging created 3D models of the residential tower, including vertical and slab reinforcement to help identify possible issues. Due to global pandemic flight restrictions, the team coordinated and conducted virtual testing in China, Hawai‘i and California.
SOLVING THE PUZZLE
“The out-of-the-box problem-solving techniques were the results of combined expertise, experience and the project team’s can-do attitude,” says Naira. “Hawaiian Dredging’s project team provided consistent communication that contributed to developing and fostering strong working relationships with the owner and the design team.”
A full-scale mockup of an exterior column was developed, including vertical and slab reinforcements. A bevy of software and hardware solutions were put to use, including Autodesk Revit building information modeling (BIM) software, clash detection tools, Autodesk BIM 360 construction management software, 4D drones and more.
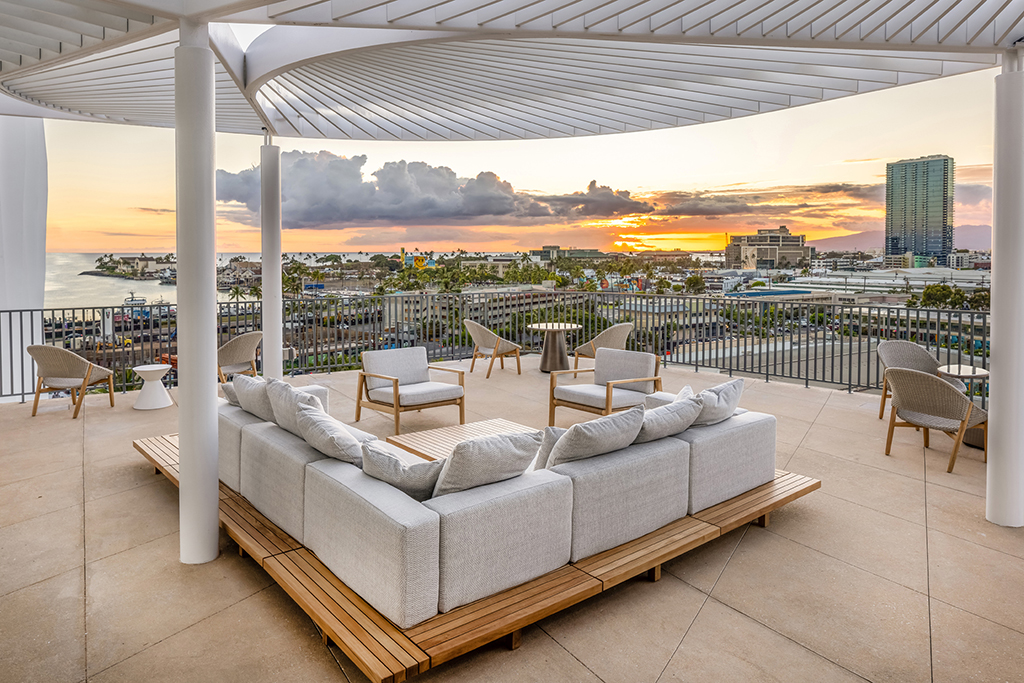
Kō‘ula residents enjoy spectacular views of Kaka‘ako and beyond from their units.
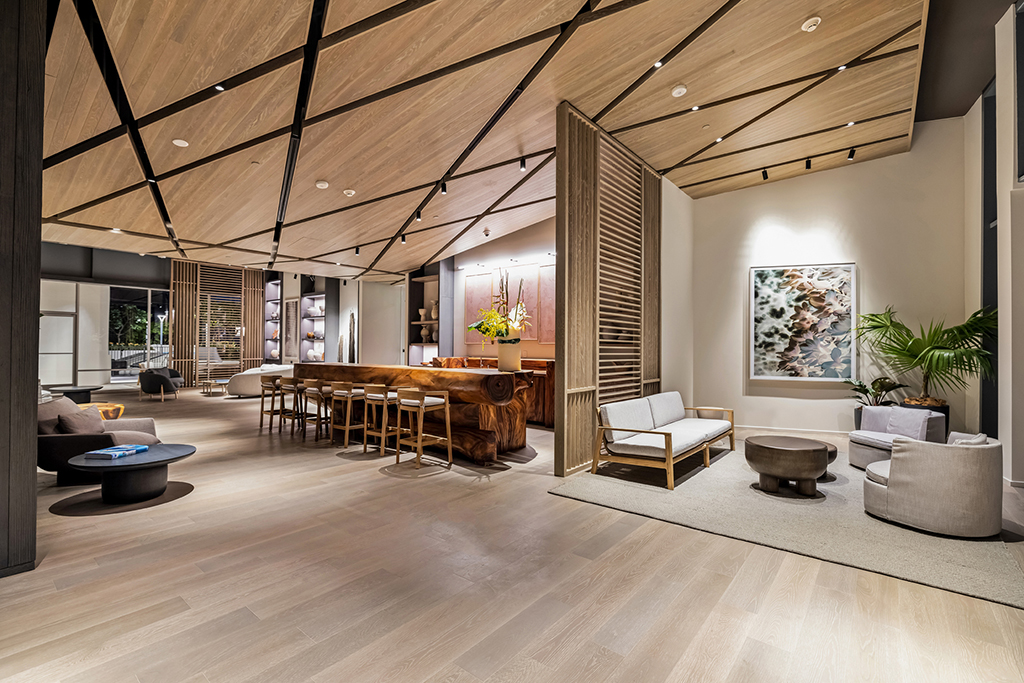
High ceilings are another feature of residential units at Kō‘ula.
“While costs for the columns were higher than conventional columns, the efficiency and simplicity of the geometry allowed for modularization,” Naira says.
The column system consists of 22 individual forms, with the tower floor plate and column geometry repeating itself every 12 floors. In order to meet design requirements, column forms were customized on lower floors and included custom forms fabricated in high-density foam for the mauka tower podium.
In addition to the structural concrete facade, there are also more than 4,000 window wall panels, of which 365 are uniquely sized. The window wall panels and sliding glass doors, combined with 2,278 balcony glass panels in 111 different sizes, complete the unique exterior design of the building.
The glass window wall incorporates so much individualized geometry that each form had to be custom-built in order to follow the building’s column pattern. More than 1,900 panels of glass (excluding sliding glass doors) were used, of which 294 were unique sizes.
Altogether, more than 2,200 lanai glass panels were installed at Kōʻula, of which 111 were uniquely sized.
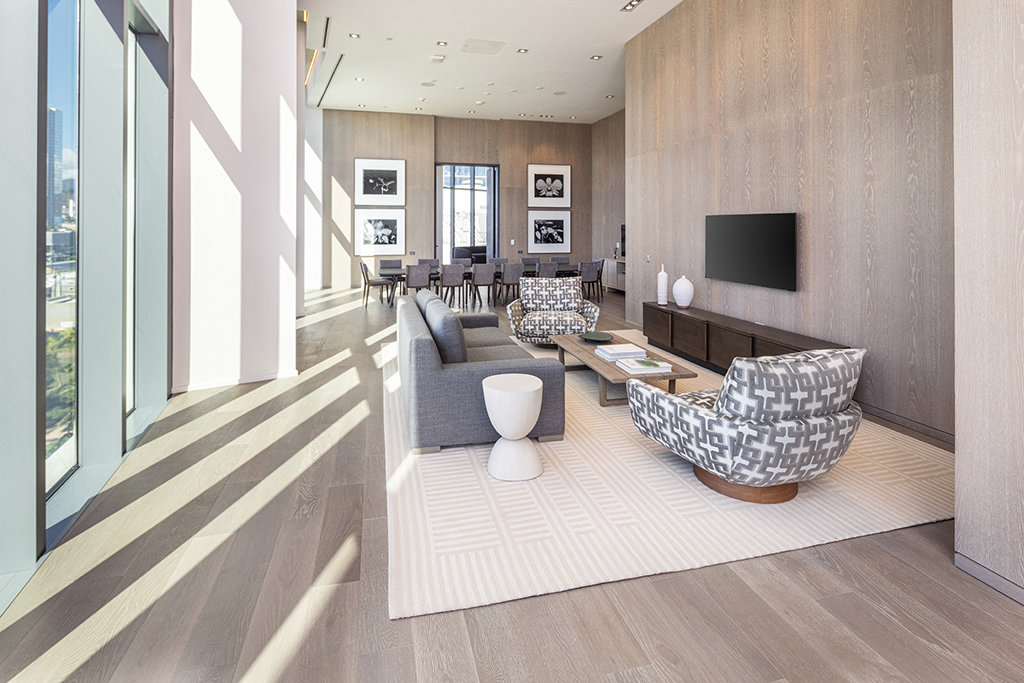
The breathtaking views at Kō‘ula are further showcased by unique glass panels incorporated into the building’s exterior design.
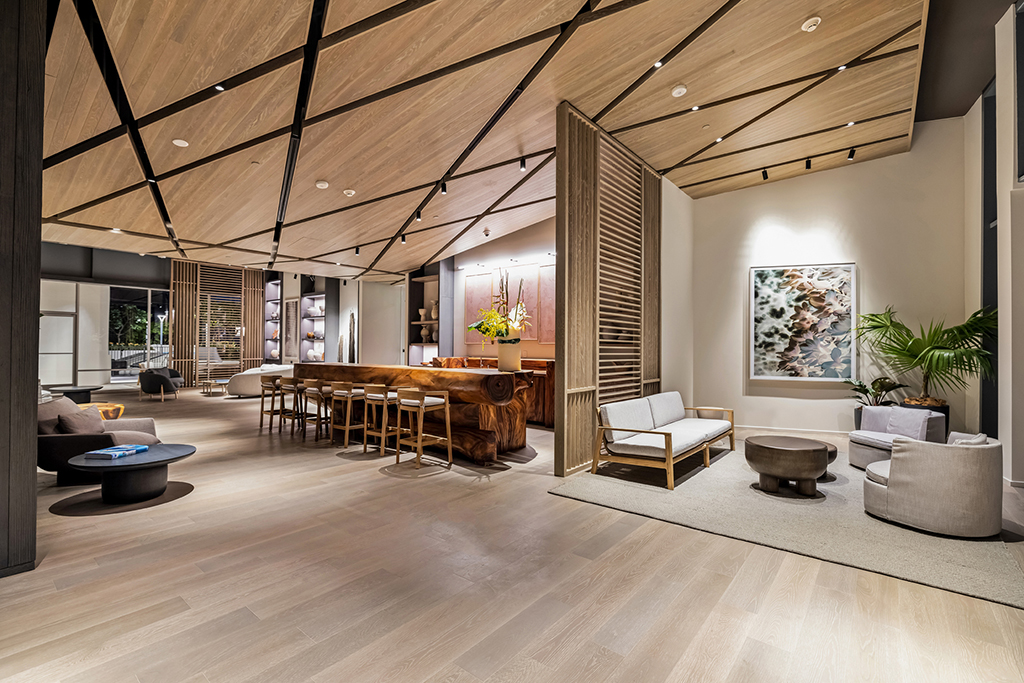
High ceilings are another feature of residential units at Kō‘ula.
“While costs for the columns were higher than conventional columns, the efficiency and simplicity of the geometry allowed for modularization,” Naira says.
The column system consists of 22 individual forms, with the tower floor plate and column geometry repeating itself every 12 floors. In order to meet design requirements, column forms were customized on lower floors and included custom forms fabricated in high-density foam for the mauka tower podium.
In addition to the structural concrete facade, there are also more than 4,000 window wall panels, of which 365 are uniquely sized. The window wall panels and sliding glass doors, combined with 2,278 balcony glass panels in 111 different sizes, complete the unique exterior design of the building.
INNOVATIONS HELP OVERCOME OBSTACLES
As was the case with many contractors, procurement was greatly affected by the global COVID-19 pandemic. Port congestion and container shortages occurred because most materials were shipped in, including the exterior window wall, cabinetry, appliances, architectural woodwork, wood flooring, countertops, stone/tile and various site furnishings.
Naira says the most impressive innovations occurred when team members finalized the project’s exterior design approach, persevered with remote testing despite pandemic restrictions, succeeded in meeting efficiently despite government and company policy limitations and utilized a novel approach to create a highly effective safety system for workers.
The Kōʻula team also initiated early procurement to earn Forest Stewardship Council (FSC) credits toward LEED Gold Certification. This certified wood credit in LEED has arguably been the most important driver of forest conservation in history, contributing to tens of millions of acres of improved management and protection. Wood that comes from an FSC-certified, responsibly managed forest is arguably among the most sustainable building materials available.
In addition, Hawaiian Dredging General Superintendent Alan Hinahara was responsible for initiating a multi-faceted review system within the company.
Every two weeks, the project team along with Health, Safety and Environmental professionals would host a question-and-answer session to review photos and notes collected by two-person teams formed by employees working on the project.
Naira says the buddy system was educational, offered valuable feedback and continued successfully through the project’s completion.
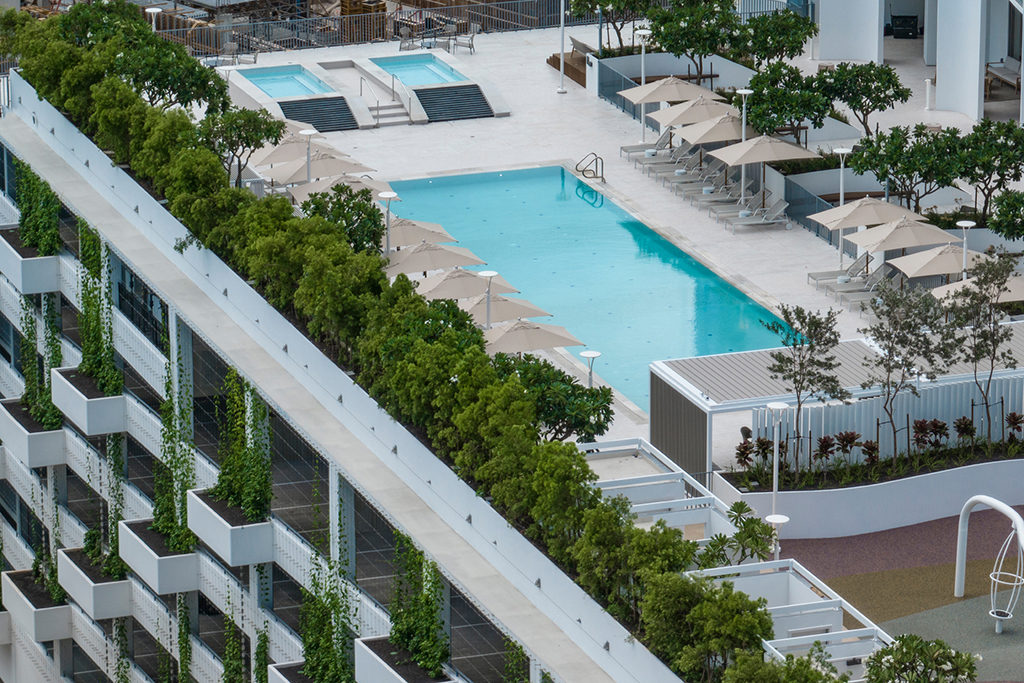
An eighth-floor amenity deck for residents includes lap and family pools, recreation and entertainment spaces, as well as outdoor dining and lounge areas.