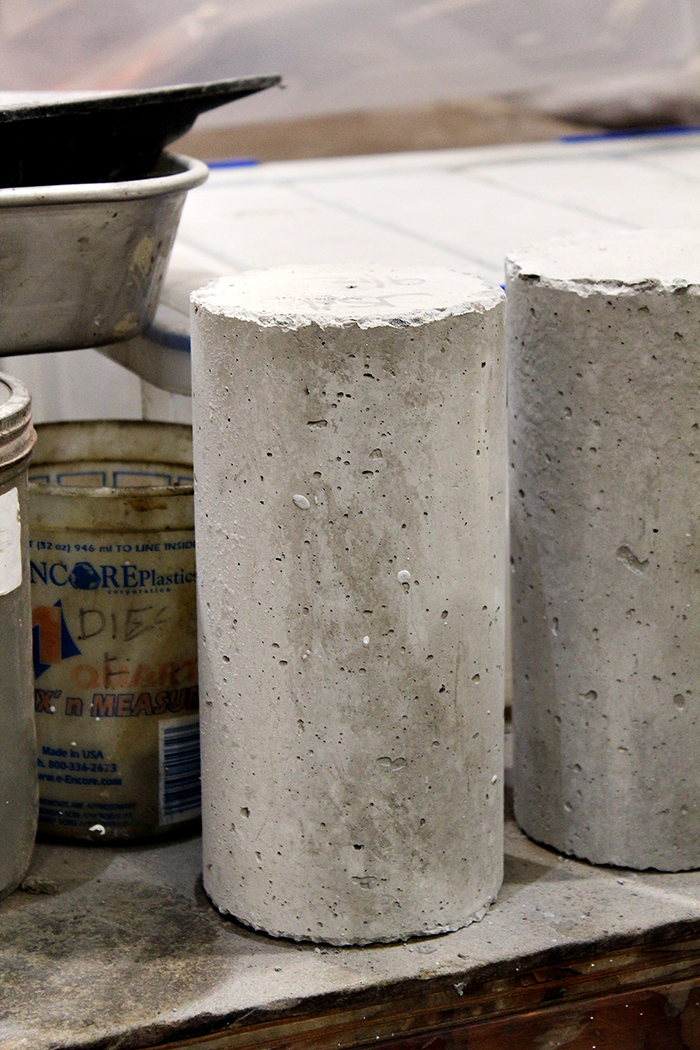
ALL PHOTOS BY VANESSA HATHAWAY
Sustainability continues to be a hot topic within the construction industry, both nationally and here in Hawai‘i.
Concrete production and usage, in particular, hinder much of the progress towards sustainable practices, as it’s the second-highest consumed product on Earth and contributes about 8 percent of total global carbon emissions, according to the Princeton Student Climate Initiative.
Although limestone-based products, like portland cement, are the most common choices across the industry, its carbon footprint during production is causing permanent damage to the environment. Some engineers, however, are taking production waste and transforming it into cement alternatives.
Enter University of Hawai‘i at Mānoa Civil, Environmental and Construction Engineering Associate Professor Dr. Lin Shen. Holding a Ph.D. in Civil and Environmental Engineering, Shen has dedicated his life to researching greener alternatives for cement, leading him to advance the production of alkali-activated concrete — a potentially cheaper and greener replacement for typical limestone-based cement.
WHAT IS ALKALI-ACTIVATED CONCRETE?
Alkali-activated concrete (AAC) doesn’t vary much from regular concrete; both are composed of a precursor, admixture, aggregate and water, but AAC employs waste material as its precursor instead of cement and uses alkali as its admixture as opposed to other chemicals.
Some cement alternatives being explored include red mud, fly ash and slag — all waste matter from construction material production.
According to Shen, the use of fly ash, red mud and slag date back to the early 1900s; however, engineers at the time lacked proper resources and technology to popularize its usage. With the concrete production process refined over the last century, engineers can now test different ingredients and methods more efficiently.
“Sometimes, the concrete will just harden within a few minutes. … If your concrete sets too fast, you cannot do mass production. So this is the kind of technical difficulty we have to overcome before we can do mass production,” Shen says. “The goal for this research is, again, large-scale mass production, high performance and also cheaper … using standard equipment.”
Concrete made with waste material has not taken off in the U.S. on a large scale yet because of the lack of standardization and resources. There are no working coal power plants in Hawai‘i, so Shen orders fly ash from Xinjiang Province to conduct his research locally.
“China happens to have 50 percent of fly ash in the world, so they have a headache trying to get rid of it,” says Shen. “So they have the willingness to do this.”
PROMISING RESULTS
To move towards commercialization, Shen and his team must ensure AAC’s functional ability matches that of current cement. To do this, Shen travels between China and Hawai‘i to gather data while running AAC through a series of assessments that test setting time, workability, slump loss, compressive strength and durability.
Aside from basic functionality tests, AAC must withstand other factors, such as sulfate attacks and other variables.
Field applications in China were successful, but Shen still had to tweak the formula to adhere to the unique weather conditions of Hawai‘i, such as high humidity, extreme heat and additional salt exposure. It all came down to adjusting proportions, concentration and contents of the admixtures, he says.
Shen’s findings show that in most categories, AAC is similar to ordinary portland cement (OPC). Another case study he later conducted revealed AAC is 29 percent stronger than OPC, reduces costs by 26 percent and cuts carbon footprints by 86 percent.
The toxic nature of waste material is still a concern, particularly red mud, stunting any large-scale testing in the U.S. Red mud contains arsenic and other pollutants that affect soil and river health if not properly controlled.
However, a field test of red mud concrete showed grasses successfully growing next to the slab, leading Shen to believe the concrete could be used in a safe way. To support his hypothesis, he conducted another series of experiments testing binding strength of concrete made with toxic waste.
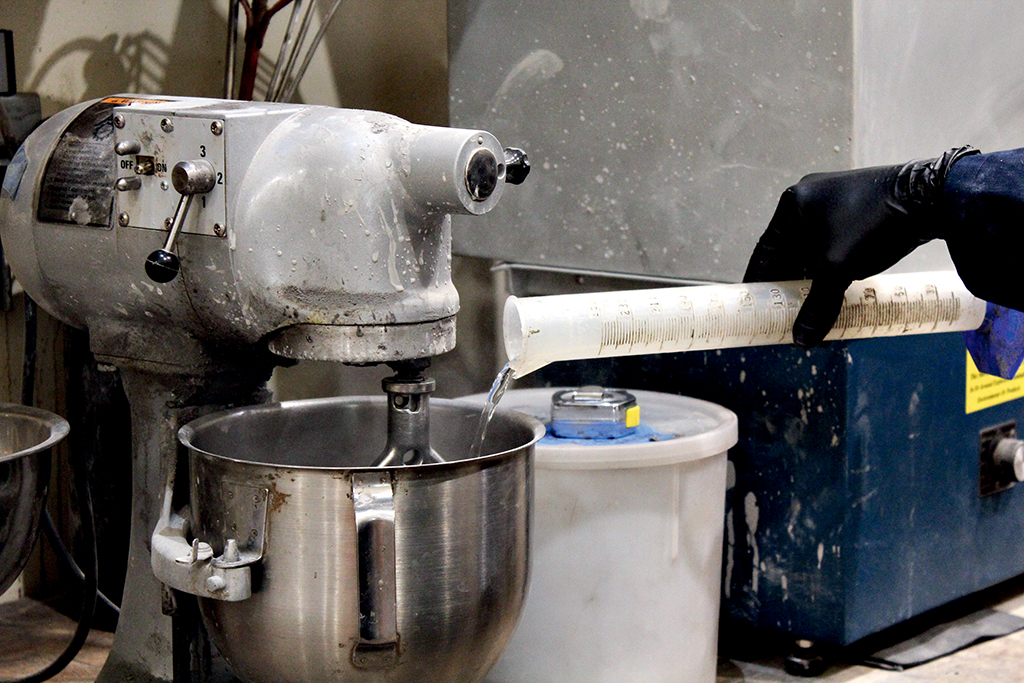
Basically, what we do is we soak the concrete made by red mud or other materials into water at different times — one day, seven days, different days — and we analyze the water,” says Shen. “How much [do] these toxic materials distort from concrete into the water? … So it just basically binds all the lead and barium inside the concrete almost perfectly, so the water passes the drinking water revelation — it’s safe to even drink the water.”
BREAKING GROUND IN THE U.S.
Equipped with the proper data, Shen has been sharing his findings with multiple committees of the American Society for Testing and Materials (ASTM), hopefully carving a path towards standardization for AAC. There have been strength-related standards already set, but the process is ongoing.
Shen is also trying to start an ASTM committee specifically for development of AAC, which requires three key players — researchers, consumers and producers.
Producers are scarce in the U.S. due to the lack of knowledge and standards of production. To find producers, more field tests need to be done, which is largely dictated by finding someone who is willing to donate land for testing.
Luckily, the Hawaii Department of Transportation agreed to a $25 million field application of AAC, with testing projected to break ground late this year or sometime in 2025. Shen will head the project.
“[Pouring] a road would be the first choice because that’s safer,” says Shen. “And that would be on the West Side, in ‘Ewa Beach.”
This would mark the first major project using AAC in both Hawai‘i and the U.S.
With the project in motion, Shen believes necessary standards for mass production could be set in as little as a year. Finding producers will be easier now that a large-scale project is greenlit and the formula has been refined.
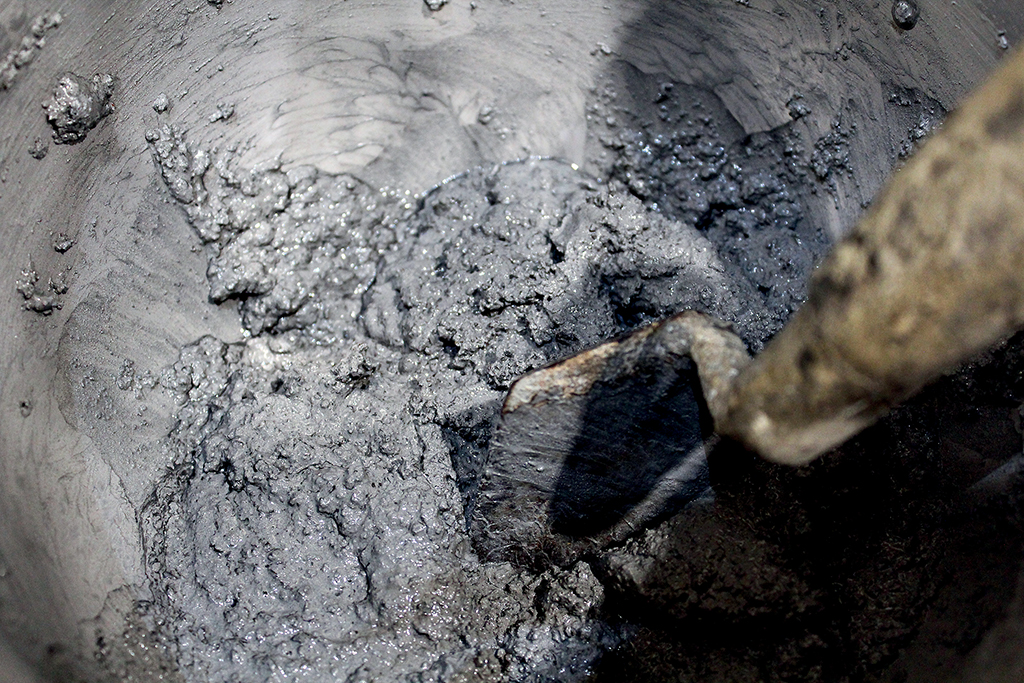
“I have a former Ph.D. student; she worked at a major cement producer in California,” Shen says. “I visited them two months ago trying to pursue them to [produce], and they seem interested.”
LOOKING TOWARDS THE FUTURE
Shen predicts within the next five years AAC could make it to the mainstream market and be used commercially, yet Shen doesn’t see sustainable concrete developments stopping there. Engineers across the board are still looking for new ways to make concrete more environmentally friendly.
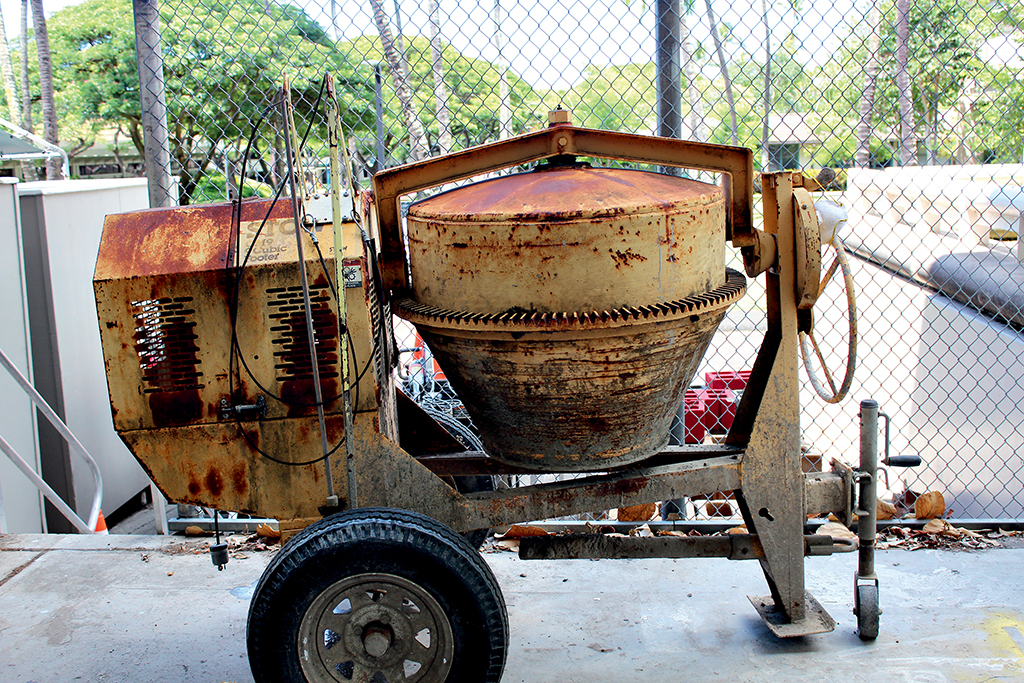
“In Hawai‘i, we use to 10 percent limestone powder … to replace to 10 percent of cement, so we can reduce to 10 percent of CO2,” Shen shares.
Shen adds engineers are also experimenting with injecting liquid CO2 in concrete to make it carbon negative.
The issue is making these types of concrete cost about the same as OPC. Because most sustainable concretes are either new to public use or still in the prototyping phases, there hasn’t been much movement towards the next step of cost-efficiency.
“In order to use the waste to replace [sand or coarse aggregate], you would have to process it,” says Shen. “You can’t just use waste and then exchange it — that’s the goal … but you aren’t able to do that yet.”
Shen believes the breakthrough needed to make sustainable concrete cheaper and more widely used is establishing standards. Until then, he plans to keep traveling between China and the U.S. to conduct more field tests and advocate for standardization.