Hawai‘i is uniquely dependent on imported goods, and Hawai‘i’s construction industry relies almost entirely on them.
A wide variety of external factors affect the costs of building materials locally, with construction lumber among the products that saw wild price spikes and fluctuations as the far-reaching impacts of COVID-19 took hold shortly after the pandemic began in the spring of 2020.
In May 2022, the U.S. Department of Agriculture’s Forest Service reported that during the first year of the pandemic, prices for wholesale plywood nearly quadrupled, which in turn saw retail prices nationwide soar from $12.80 per sheet to $48 per sheet.
LUMBER COSTS EASE
Lumber prices nationally are approaching pre-pandemic levels, and Hawai‘i has seen the same kind of relief from exorbitant lumber costs despite importing virtually all of its building materials from out of state.
The National Association of Home Builders reports that as of April 19, the price of lumber futures fell by 16.7 percent in the previous month, and the prices of western fir, southern yellow pine and oriented strand board saw modest decreases as well.
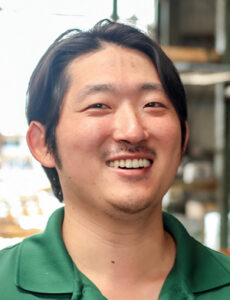
BEYOND SUPPLY AND DEMAND
“Although lumber prices have stabilized from the dramatic peaks experienced during the pandemic, they are anticipated to rise in the forthcoming years,” says HPM Building Supply lumber buyer Danny Matsuura. “Data from the USHMC (United States Housing Market Conditions) indicate a consistent rise in housing demand, as evidenced by the upward trend in new home sales from 2011 through 2023.”
Soaring lumber prices during the pandemic can be most easily attributed to dramatically increased demand paired with a crippling supply shortage due to stifling bottlenecks in the supply chain.
Those obstacles have largely been overcome in the years since the peak of the pandemic, but other market forces can have as much of an impact as supply and demand.
“At the federal level, the Federal Reserve interest rate and the upcoming presidential election are poised to influence construction lumber prices over the next year,” Matsuura explains. “While the election itself may not directly affect lumber costs, any subsequent policy changes could impact interest rates, tax regulations and economic strategies, thereby indirectly influencing the housing market and, as a result, lumber prices.”
One of the most influential factors in Hawai‘i lumber prices — oil prices — has roots on the other side of the world. Rising prices have a significant impact on the cost of lumber internationally.
Hawai‘i is particularly vulnerable to rising fuel costs regardless of the actual supply and demand dynamic of lumber supply.
When fuel prices rise, so do prices for all Hawai‘i imports. The more it costs to import construction lumber and transport those materials to projects throughout the state, the more those costs ultimately find their way into the pockets of Hawai‘i’s homebuilders.
Raw inflation is also a major factor in lumber and construction costs.
“Inflation is affecting the cost of everything,” says Scott Loomer of Truss Systems Hawaii. “The cost
of raw materials, mainland labor, trucking, fuel and shipping are
increasing the ‘landed costs’ of all
our materials, and of course we have all the same factors here in Hawai‘i once it arrives.”
PREPARING FOR RISING COSTS
Hawai‘i’s lumber suppliers have weathered the storm of price spikes that resulted from the pandemic. The industry tumult caused by supply shortages became an opportunity to reevaluate the marketplace, and to make adjustments in the event of more drastic lumber price jumps.
“I think we learned a lot during the pandemic with regards to price and inventory controls to better protect ourselves and our customers to help mitigate the drastic price swings,” says Loomer. “However, there is only so much we can do in Hawai‘i.”
Matsuura is similarly circumspect about the lasting impacts and lessons learned through the pandemic.
“Given that lumber prices fluctuate weekly, we encounter challenges as suppliers in managing the escalating costs of materials,” he says. “As one of the primary importers into Hawai‘i, we strive to purchase directly from lumber mills and manufacturers, aiming to reduce expenses for our local builders.”
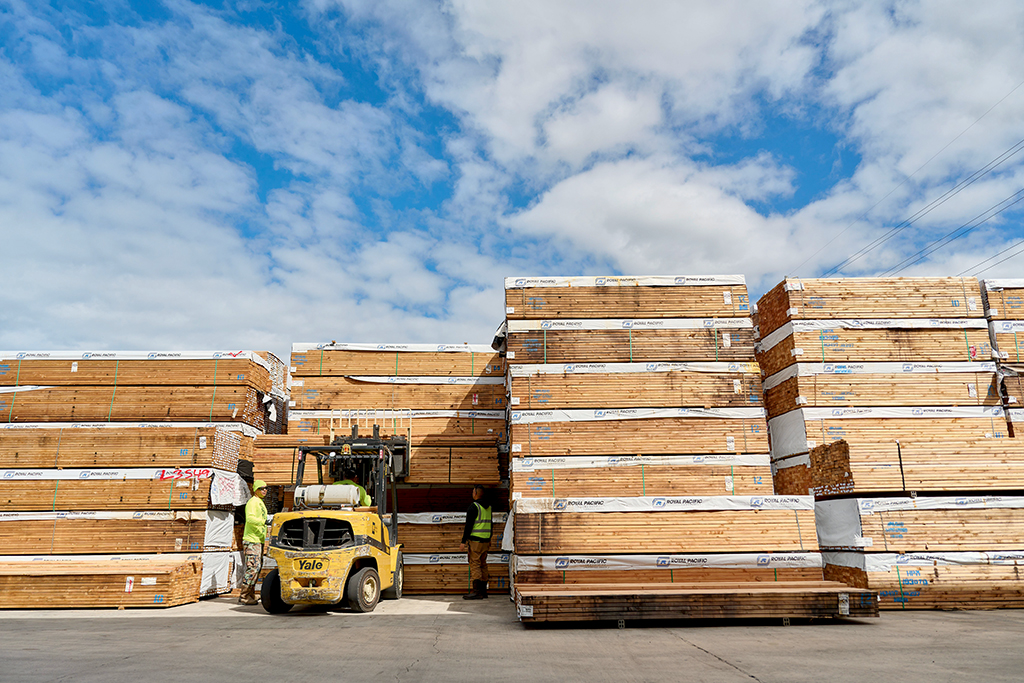
ON THE FRONT LINES
Lumber costs are often regarded from a macroeconomics perspective (supply and demand, fuel prices, labor costs, inflation, etc.). But Hawai‘i’s construction contractors and their clients experience the on-the-ground implications of global supply chain and price fluctuations.
Kevin Muir of United Pacific Builders says complications and conflict arise when an estimate for lumber costs based on current projections are dwarfed by skyrocketing costs after a contract is signed.
“Some of the jobs that we already had on the books were priced out pre-pandemic,” he says. “All of a sudden they don’t start until after the price hike … so we have to somehow explain [the lumber price] to the client.”
To accommodate the increases, contractors now list “exclusions” in their bids, limiting the durations of estimates to 30 days, for example.
WHAT TO WATCH FOR
There are a number of factors that are likely to influence the constantly fluctuating price of lumber in Hawai‘i.
New restrictions are set to be put in place by the Oregon Board of Forestry, converting 630,000 acres of forest into conservation lands.
“This move is forecasted to slash the annual lumber supply by about 18 percent,” says Matsuura.
Potential interest rate cuts by the Federal Reserve will also play a key role in demand for new home construction, which will increase lumber demand and prices as home construction becomes more attractive.
Similarly, inflation will impact the price of lumber in Hawai‘i directly. Increasing tension in the Middle East could result in a strategic cut in oil production, which will have a direct impact on shipping costs for construction lumber to Hawai‘i, as well as the cost of interisland transport and on-island materials trucking.
In order to be prepared for future, possibly dramatic increases in the cost of lumber in Hawai‘i, local lumber suppliers, construction
contractors and future homeowners should look at national and international developments to best gauge the ever-changing lumber market and plan ahead accordingly.