Technological evolution has skyrocketed within the last century — and that includes the construction industry. Now, with the evolution of artificial intelligence (AI), there are more avenues for innovating planning and executing projects.
A common misconception is that AI will replace the need for physical workers. However, many experts refute this claim, as they’ve found AI’s role in the construction process is meant to save time, not replace human input.
Estimating, project management, scheduling and mapping are among the more popular AI-assisted functions that are currently being researched and tested, but AI has the potential to eventually touch all aspects of construction, from safety checks to sustainability.
EXPEDITED ESTIMATING
AI-assisted estimating is one process that’s gaining in popularity. Various companies are expanding their estimating services by monitoring trending technological methods and developing AI software accordingly, such as linking available inventory to local retailers.
A current hurdle is the lack of machine-learning capabilities in most AI software. AI can pull potential estimates from local suppliers based on a set list of project criteria, but cannot make suggestions based on additional information, such as specific client requests or difficulties acquiring certain materials.
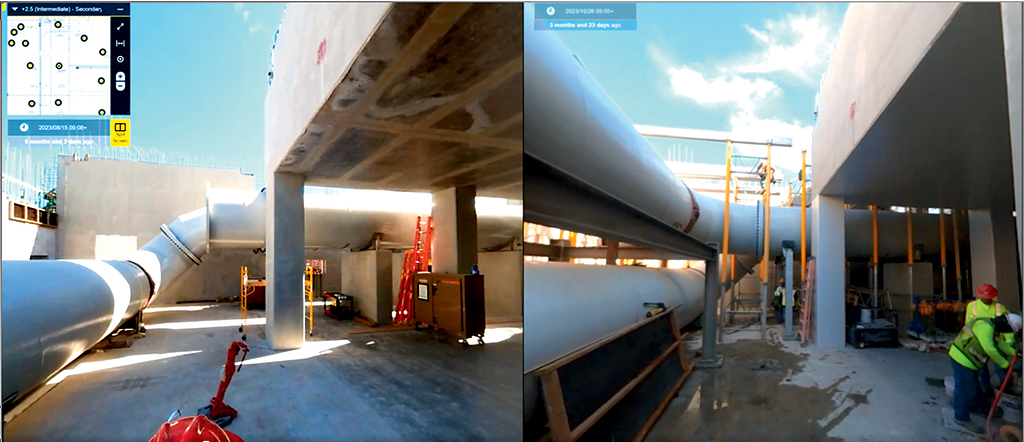
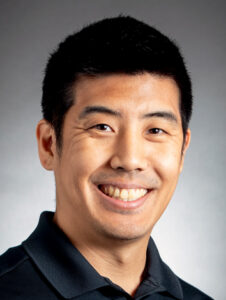
“When machine learning starts becoming part of the construction software, that’s when it’s going to be a big change,” says Albert C. Kobayashi Inc. Senior Project Engineer Chase Hiyakumoto.
According to an 2023 market trends analysis report by The Insight Partners, the market size for cost-estimating software will reach approximately $3.89 billion by 2031 — with AI contributing substantially to that growth.
“Traditional cost estimation models frequently rely on manually picked characteristics, which are time-consuming and prone to bias. However, the use of technologies such as artificial intelligence and machine learning (ML) can considerably improve the precision of cost estimates by providing more accurate projections,” the report says.
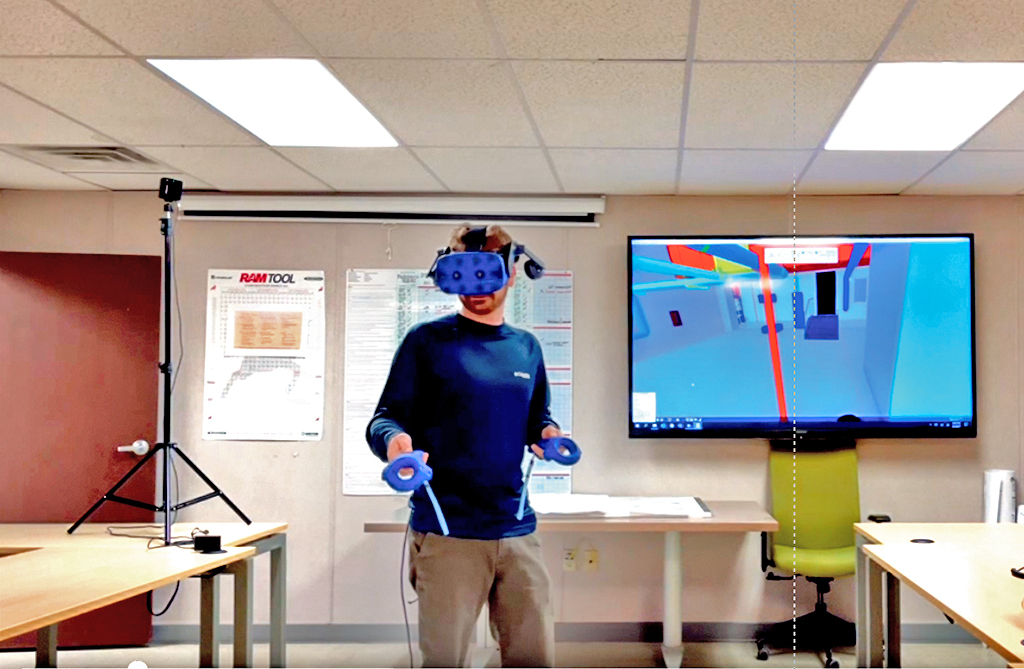
MAPPING IT OUT
Laser scanning has been around for a few years, but some companies are elevating virtual mapping by enhancing its abilities with AI and time-tracking software, allowing contractors to compare images and mark progress.
Many companies use drones for outdoor imaging and have workers walk through interiors with cameras attached to their hardhats for indoor imaging. All images can then be uploaded to software that has specialized functions.
“This is the kind of thing that our software will come in and say, ‘This is the pipe that was installed on this day, this pipe was installed on this day,’ and be able to go mark up drawings and show that kind of thing,” Construction Manager Drew Rebman explains.
The real challenge is making the data compatible with mobile devices. Due to the detail of the images, the tracking software typically requires a large computer that has the capacity to support and run it; but this limits the availability of the images, forcing contractors to view them at a single location rather than being able to move freely between office and worksite.
Recent developments have allowed the data to be uploaded on a mobile device, making viewing and distribution much easier.
“So we can go and capture this data … and get that out to the masses to go do those quality control checks, to go do those existing condition evaluations on how we’re doing to go demo[lish] a building and how we’re going to go tie into an existing building,” says Rebman. “At the end of the day, we need to be safer and … faster, so we can go use things like [mobile virtual mapping] to go help us along.”
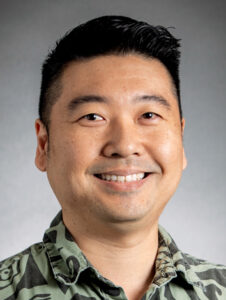
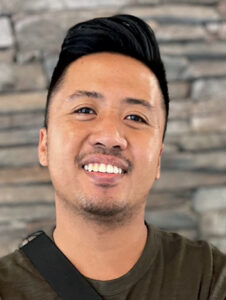
PERSONAL AI ASSISTANT?
Researchers across the industry are experimenting with scheduling AI, generating approximate project timelines, prices and potential challenges, among other variables. Contractors occasionally still must manually input or edit criteria, but the software has already yielded promising results.
According to Chivas Miho, Moss & Associates director of preconstruction, his colleagues at Hawaiian Dredging Construction Company Inc. have already utilized a scheduling AI software developed by Alice Technologies.
“[The software] tells you, ‘Okay, you’re 60 percent done with the walls, but your schedule says you’re supposed to be done with 80 percent of walls. In order to meet schedule, you have to either … work OT this many days with this many people or bring in five more guys to the schedule,’” says Teo Samilin, Swinerton preconstruction manager. “So [AI’s] good in that sense, it catches all the big things, but not the small things … but at the end of the day, there’s promise in the program.”
However, most companies have not adopted scheduling AI software due to the cost for both the software and an additional operator not producing a solid return on investment.
“It requires a full-time engineer kind of, updating it daily. So to justify the additional personnel for the program — and it’s not just for scheduling — [but] to see all their other [possible mistakes] too … it doesn’t make it feasible yet,” Miho cautions. “In time, it’ll certainly be.”
CRITICAL CONCERNS
Although AI has the potential to expedite construction projects, some remain apprehensive about its normalization. The main concern is that younger generations of workers might rely too heavily on AI instead of learning essential skills through trial and error.
“For [younger workers] to say, ‘Oh, well this happened on these other projects, so I should be careful.’ I think that’s the kind of thing that comes with the older generation — [it’s] experience level,” says Miho. “Seeing what happened in the past that went wrong. … the younger gen is definitely eager and excited to learn about it, but I think without the previous experience, they’re not sure what … they’re looking for, as far as dangers that could happen.”
But it seems like most of these concerns have time to be discussed, as generations who grew up using AI still have a few years before they’re ready for the workforce.
“I think still the people who are coming out of college that might’ve used it to get through still had to go through high school without it,” says Hiyakumoto. “I don’t think we’re there yet, experiencing any lack of critical thinking due to AI.”
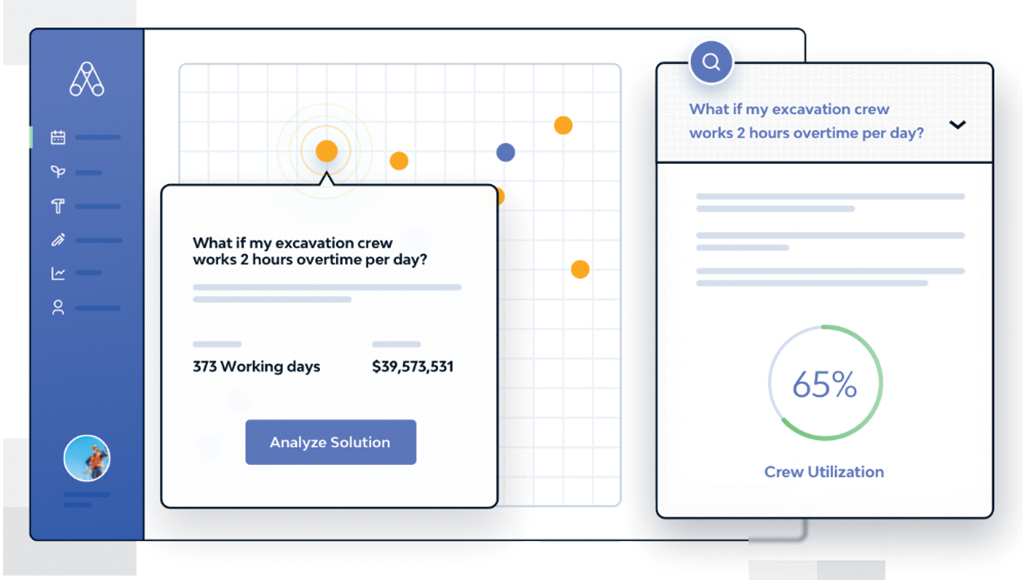
THE FUTURE OF AI
Before AI software can be fully integrated into the construction industry, it needs to produce higher accuracy, eventually adapting to machine-learning.
Procore recently showcased their new software, Copilot, which can generate a request-for-information (RFI) based on a searched topic or item. Copilot can also create follow-up RFIs based on the results and even write RFIs for contractors. Copilot also features unique “Agent” functions that handle preconstruction operations like submittals and scheduling. The software will be available sometime in 2025.
Although the interest in developing AI is high, some predict widespread adoption will be slow, as the industry must decide where AI fits within their operations and what kind of training workers will need to oversee the software in varying positions.
“I mean, even in the pre-constructing estimating for us, I think the best [AI] can do is just shorten the manual procedure time,” says Miho. “So maybe you don’t need somebody doing takeoffs as long, but they still have to be able to … spend a tremendous amount of time trying to understand what the numbers mean.”
For now, companies are continuing to rely on their experienced workers to complete jobs while still working towards an AI-assisted future.